SHELL AND TUBE
HEAT EXCHANGERS
Shell and tube heat exchangers are integral components in the Metal Finishing industry, where precise temperature control of chemical baths is crucial for processes like electroplating, anodizing, and pickling.
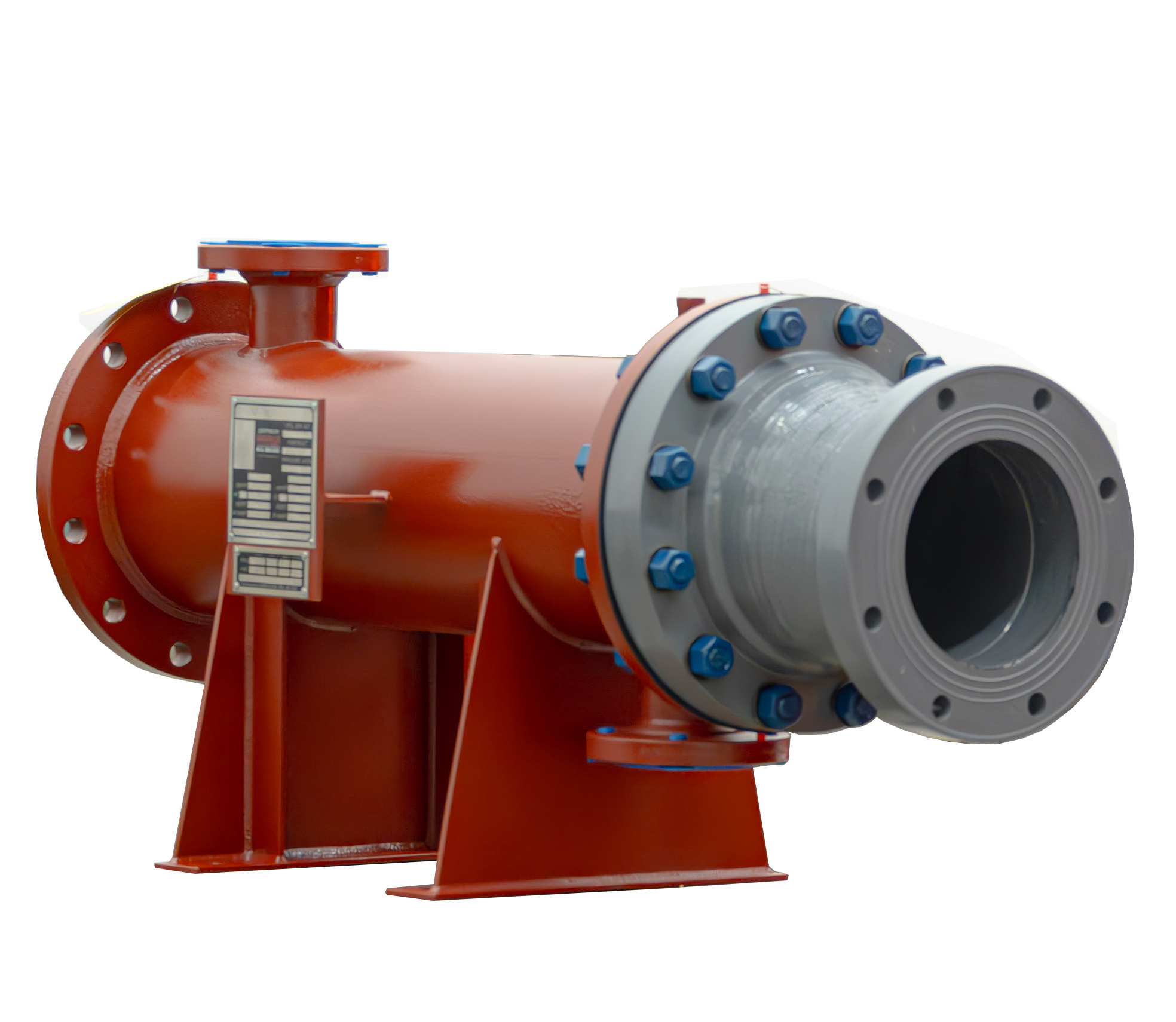
Shell and Tube Heat Exchangers: An Essential Component in Metal Finishing
In the Metal Finishing industry, maintaining optimal temperature control during various processes is crucial for achieving high-quality results. One of the most effective and reliable methods to manage thermal energy is through the use of shell and tube heat exchangers. These devices are engineered to transfer heat between two fluids efficiently, ensuring consistent processing conditions.
Shell and tube heat exchangers are widely used in various industrial applications. Metal Finishing processes often require precise temperature control for solutions used in plating, anodizing, or other surface treatment processes. Shell and tube heat exchangers are effective in maintaining these temperature controls due to their robust design and high efficiency.
shell and tube heat exchanger
construction and operation
shell and tube heat exchanger construction and operation
Structure:
Tubes: These are the primary channels through which one of the fluids flows. The tubes can be made from a variety of materials, including Stainless Steel, Zirconium and Titanium, chosen based on their thermal conductivity and resistance to corrosion.
Shell: The outer casing that contains the tubes and holds the other fluid. The shell is usually made from robust materials like carbon steel or stainless steel to withstand high pressures and temperatures.
Tube Sheets: These plates secure the tubes in place and provide a seal between the shell and the tube fluids.
Baffles: Installed within the shell to direct the flow of fluid over the tubes, enhancing heat transfer efficiency by promoting turbulence.
Function:
The operation of a shell and tube heat exchanger involves two fluids at different temperatures. One fluid flows through the tubes while the other flows around the tubes within the shell. Heat transfer occurs through the tube walls, either heating or cooling the fluid inside the tubes. Depending on the application, the fluids can flow in the same direction (parallel flow) or in opposite directions (counterflow), with counterflow arrangements generally providing greater efficiency.
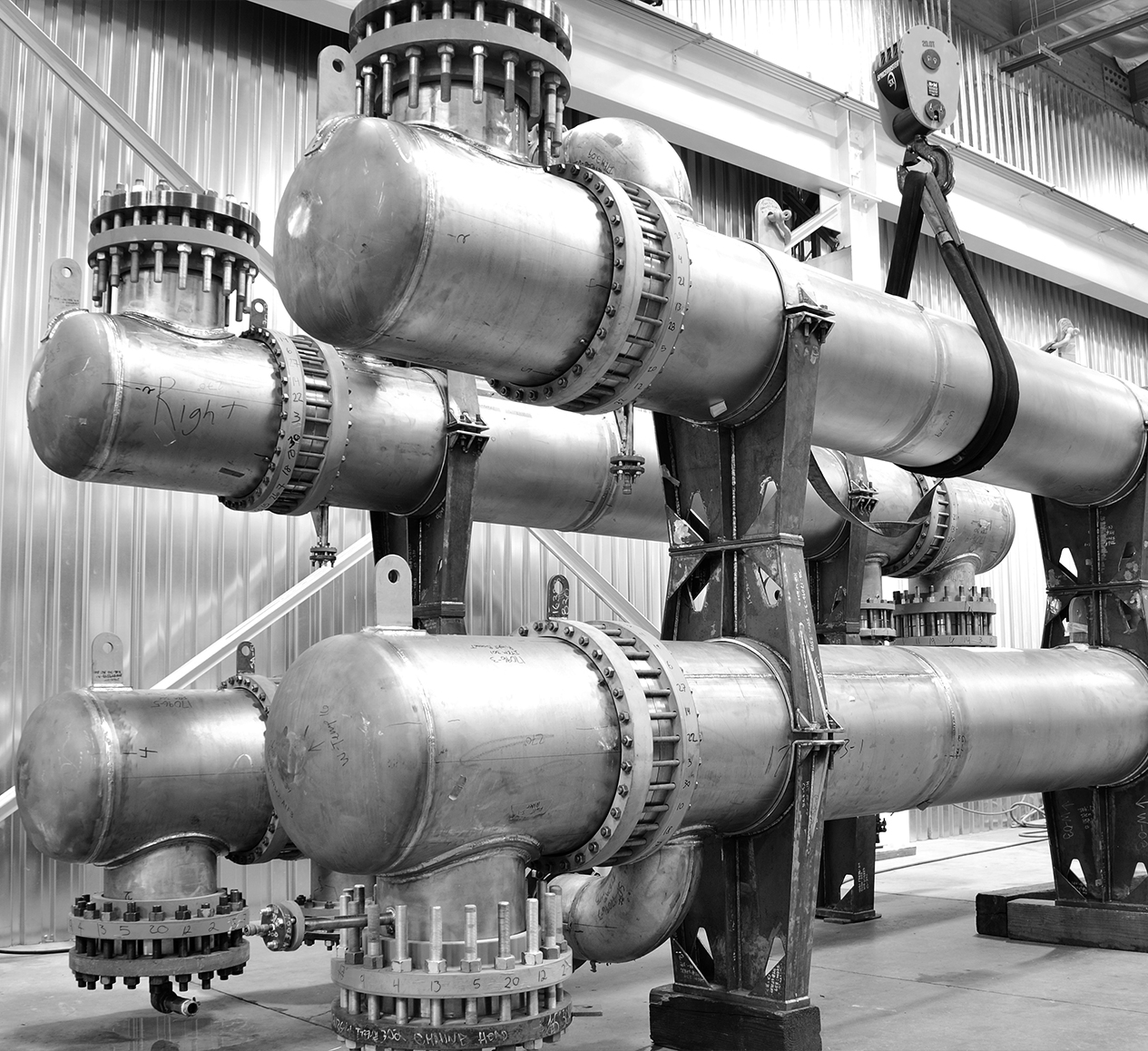
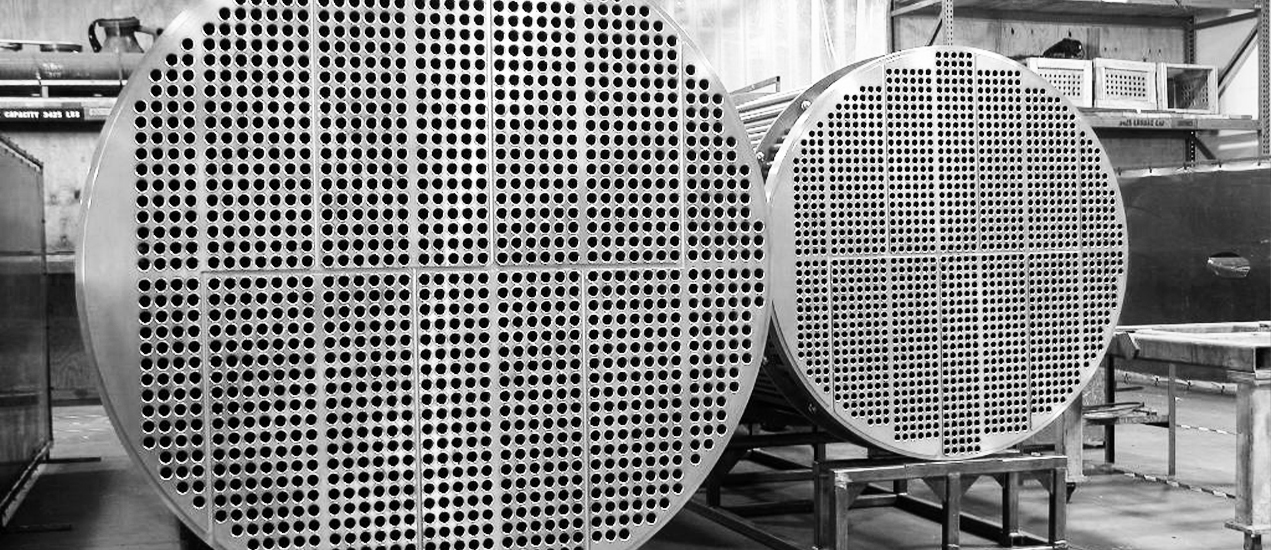
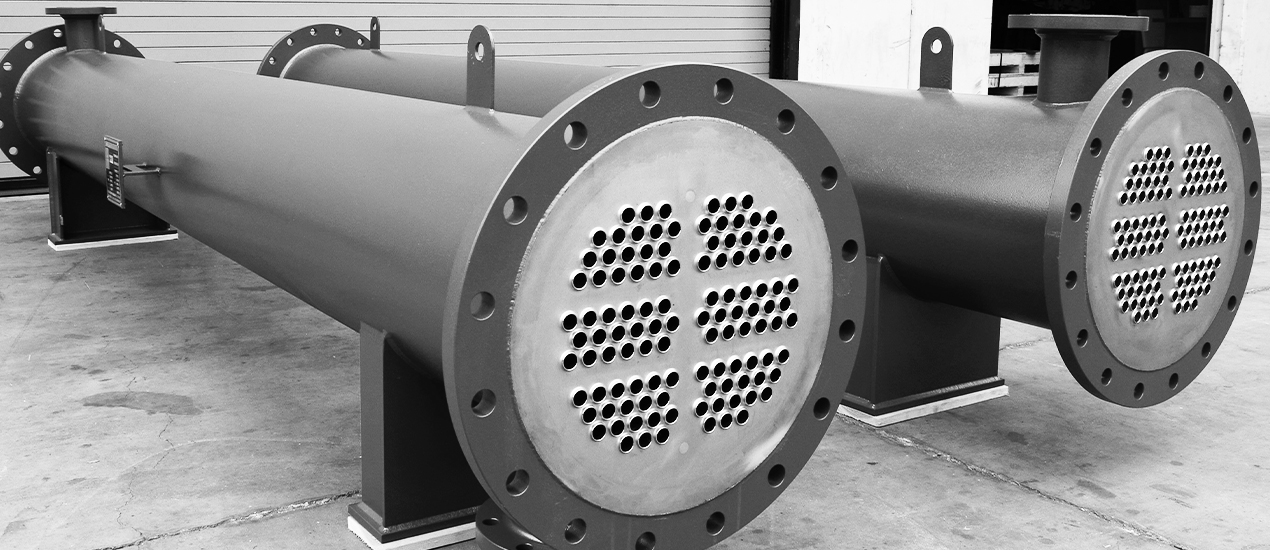
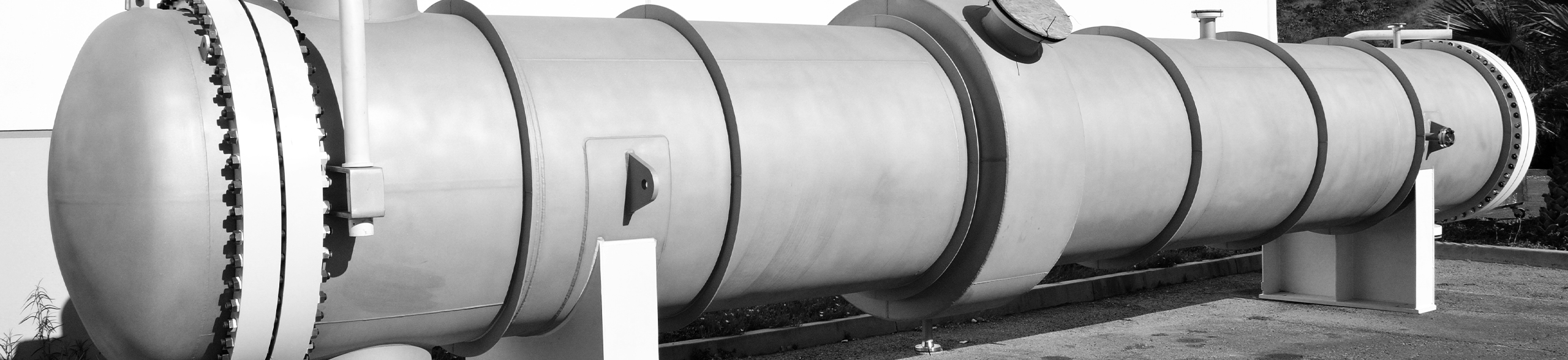
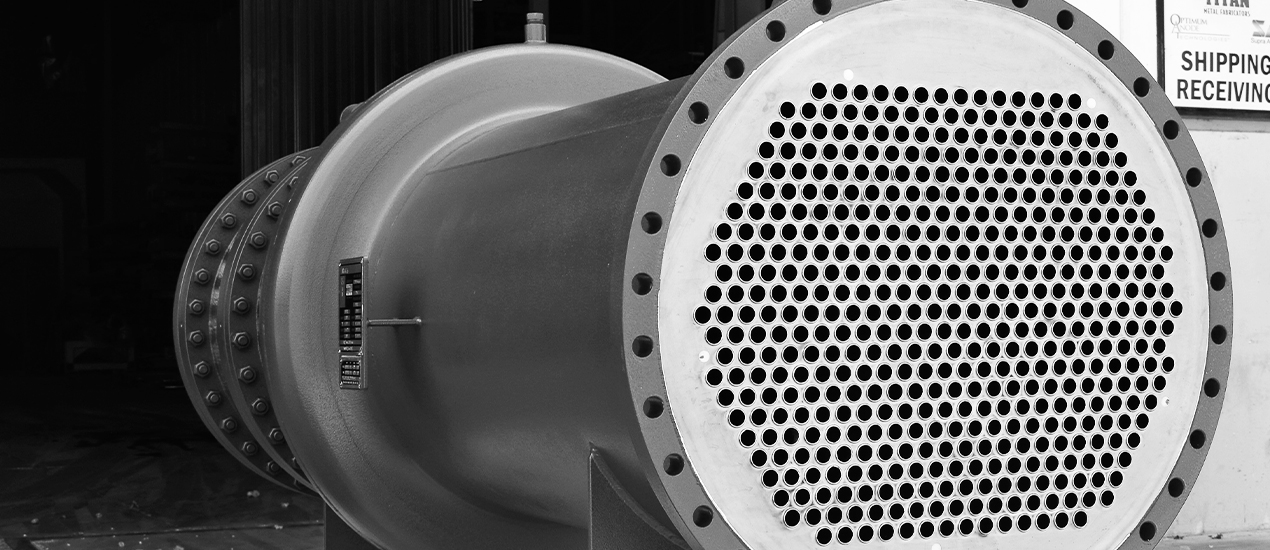
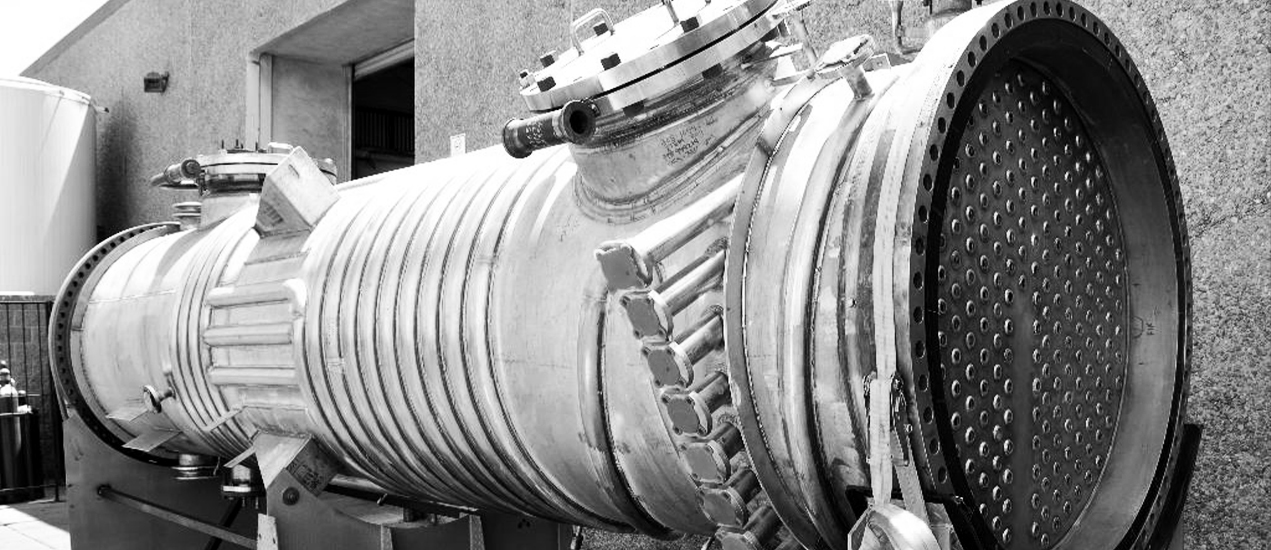
Benefits of Shell and Tube Heat Exchangers
Efficient Heat Transfer: The large surface area of the tubes allows for effective heat exchange, essential for processes such as electroplating, anodizing, and chemical baths.
Durability and Reliability: Constructed from corrosion-resistant materials, these heat exchangers can withstand harsh chemicals and extreme temperatures common in Metal Finishing.
Scalability: Available in various sizes and configurations, shell and tube heat exchangers can be tailored to fit small-scale operations or large industrial facilities.
Ease of Maintenance: The modular design facilitates easy inspection, cleaning, and replacement of parts, minimizing downtime and maintenance costs.
Applications in the
Metal Finishing industry
Shell and tube heat exchangers play a critical role in several Metal Finishing processes:
Electroplating: Maintaining consistent bath temperatures ensures uniform coating thickness and quality.
Anodizing: Precise temperature control is essential for achieving desired oxide layer properties.
Chemical Etching: Regulating temperatures enhances the precision and speed of the etching process.
Cleaning and Rinsing: Efficient heat transfer improves the effectiveness of cleaning and rinsing baths by maintaining optimal temperatures.
technical resources
You’ll find product information, reactive metals information, corrosion charts, calculators and much more in the TITAN Technical Resource Center.
experts in the shell and tube
heat exchangers industry
Shell and tube heat exchangers are indispensable in the Metal Finishing industry due to their efficiency, reliability, and versatility. By providing precise temperature control, they enhance the overall productivity of Metal Finishing operations. Investing in a robust shell and tube heat exchanger can lead to significant improvements in process control and operational efficiency, making it a wise choice for any Metal Finishing facility. For more information on selecting the right shell and tube heat exchanger for your needs, contact our team of experts today!