TITANIUM RACKS
Titanium racks are an excellent choice for Metal Finishing operations seeking reliability, efficiency, and long-term cost savings.
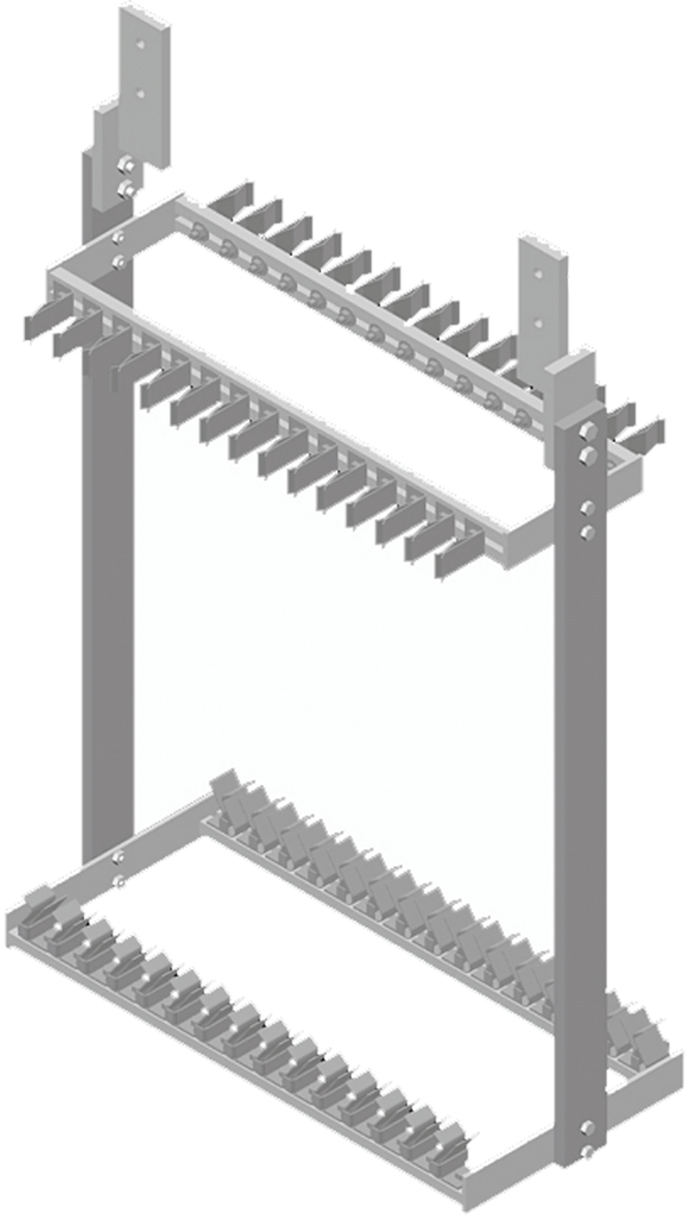
Titanium Racks: Superior Solutions for Metal Finishing
In the Metal Finishing industry, the choice of materials and equipment can significantly impact the quality, efficiency, and durability of the finishing process. Titanium racks have emerged as a preferred solution due to their exceptional properties, offering numerous advantages over traditional materials. This explores the benefits, applications, and reasons why titanium racks are an excellent investment for metal finishing operations.
Their superior corrosion resistance, strength, and temperature stability make them suitable for a wide range of applications, ensuring high-quality finishes and enhanced productivity. Investing in titanium racks is a strategic decision that can significantly improve the performance and longevity of your Metal Finishing processes.
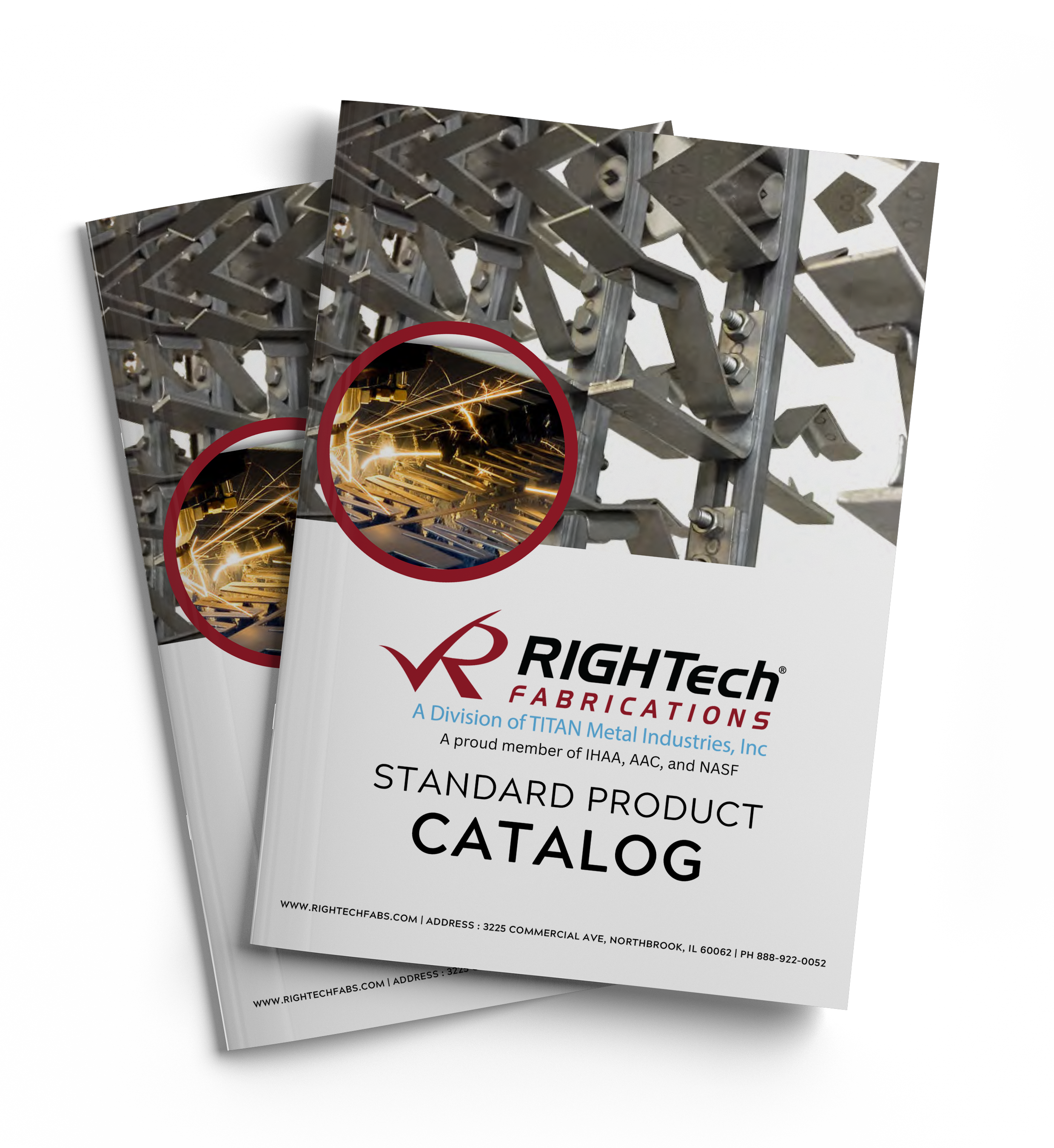
RIGHTECH BROCHURE
Find the latest product information, for high quality anodizing and plating equipment in our new RighTECH brochure. We are the industry leader in the design and fabrication of racks, baskets, and coils for metal finishers.
titanium racks
technical details
Titan Metal Finishing box, disc, and utility racks are being widely used in the Anodizing industry, as they combine high versatility for the racking of many different parts with economy, productivity, and precision.
splines/ hooks
disc racks
collars
box racks
utility racks
Clips & Clamps
FASTENERS
Hi-Lode Racking System
types of metal finishing for titanium racks
Anodizing:
In anodizing processes, titanium racks provide stable support and maintain their integrity even in the aggressive electrolytic solutions. This ensures the production of high-quality anodized layers with uniform thickness and color.
Chemical Processing:
For processes involving harsh chemicals, such as etching and cleaning, titanium racks offer unparalleled corrosion resistance, ensuring they remain intact and functional over multiple cycles.
Electroplating:
Titanium racks are ideal for electroplating due to their excellent conductivity and resistance to the acidic and alkaline solutions used in the process. They ensure uniform current distribution, resulting in consistent coating thickness and quality.
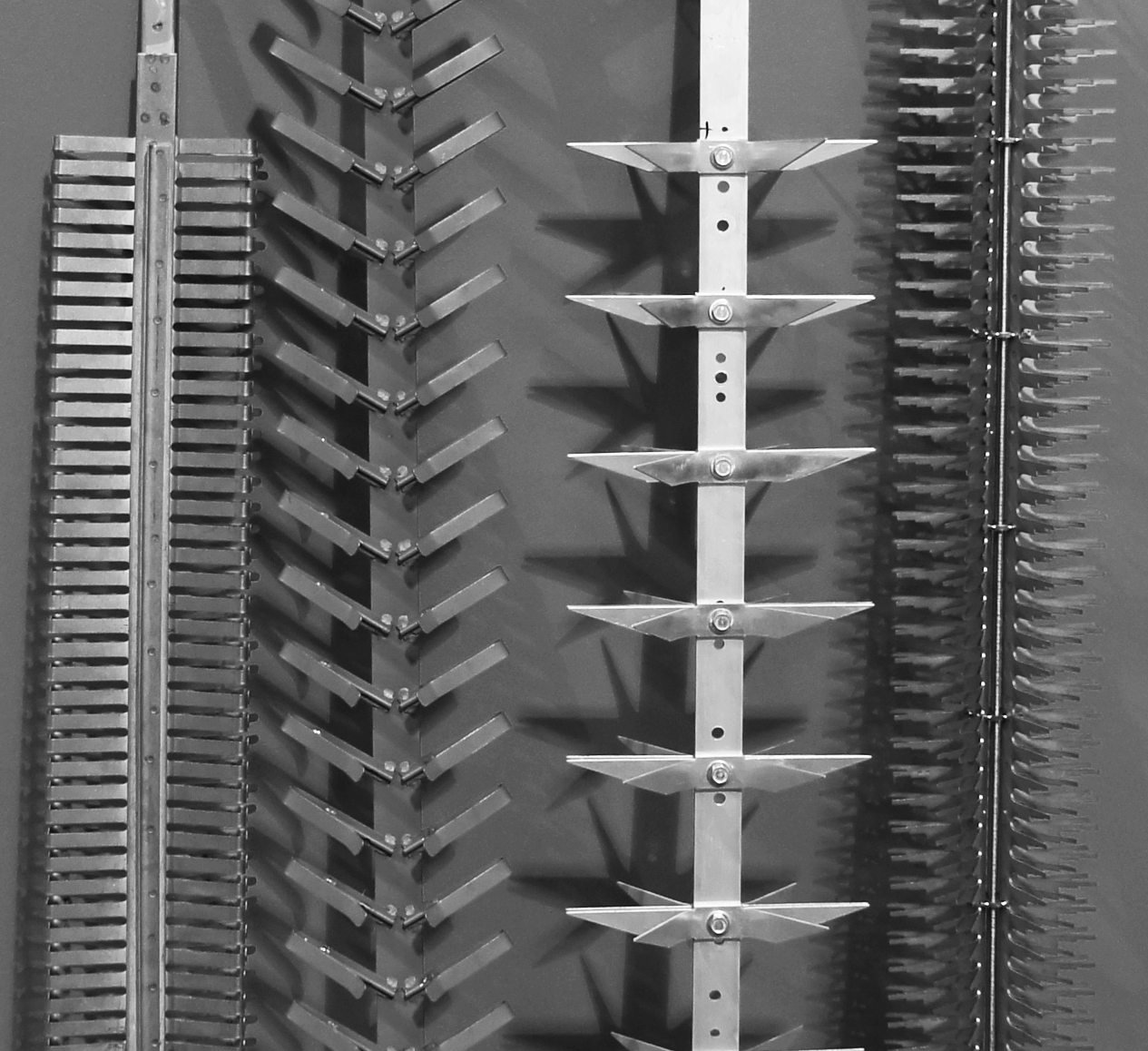
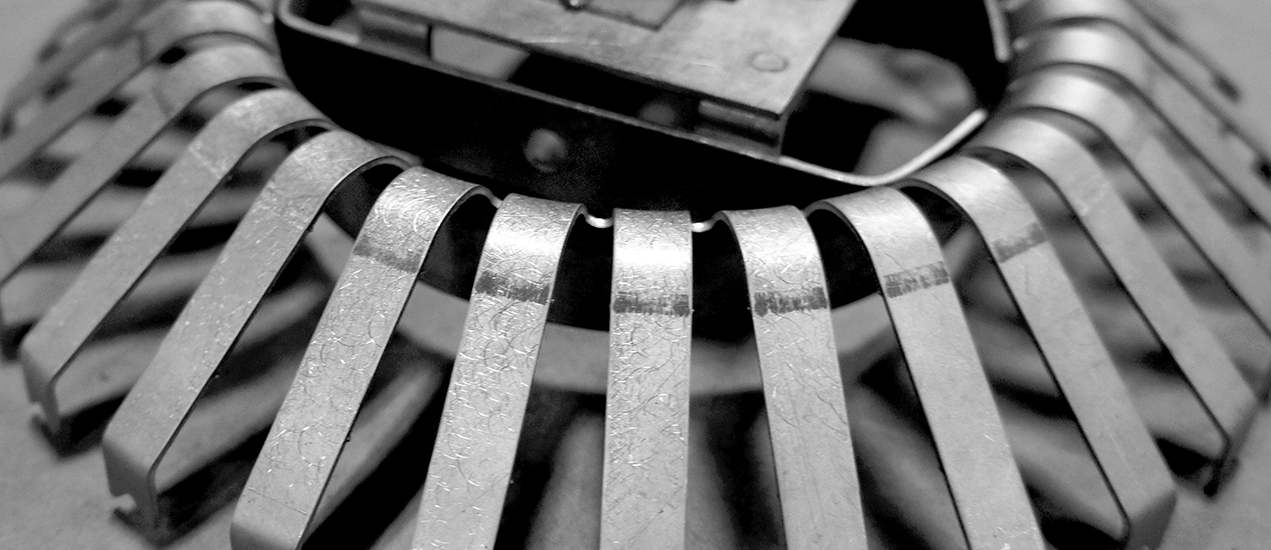
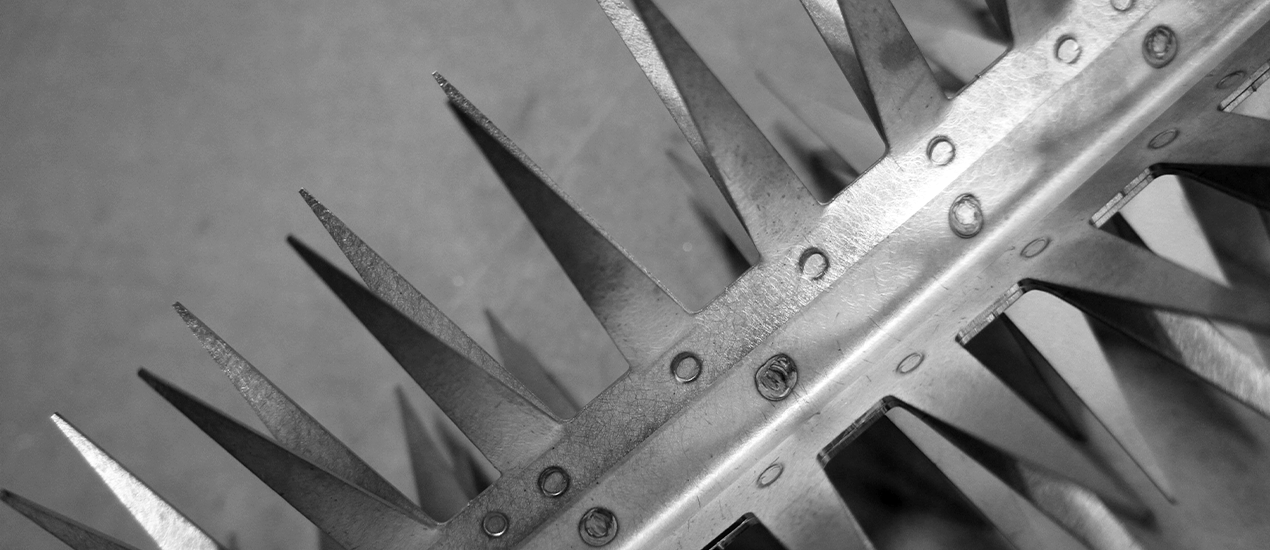
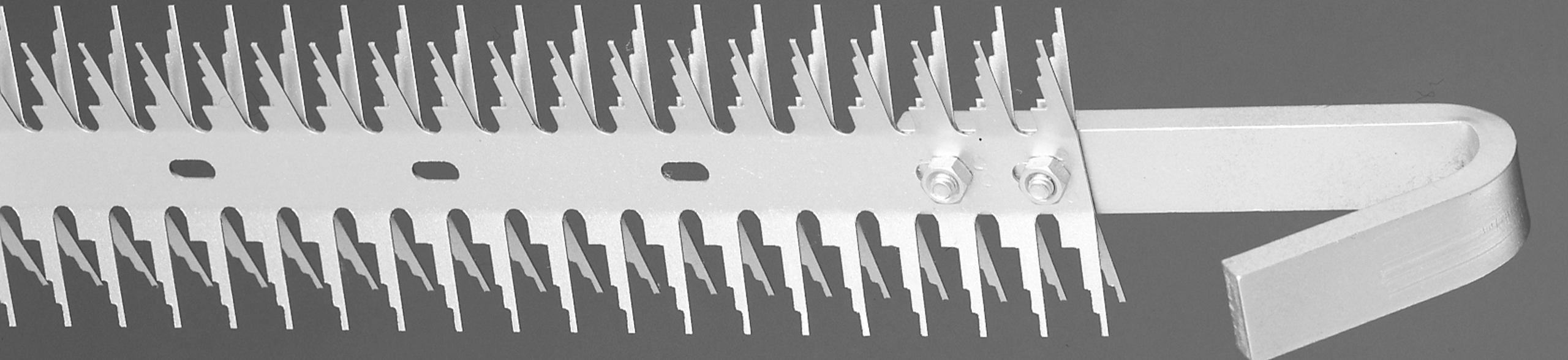
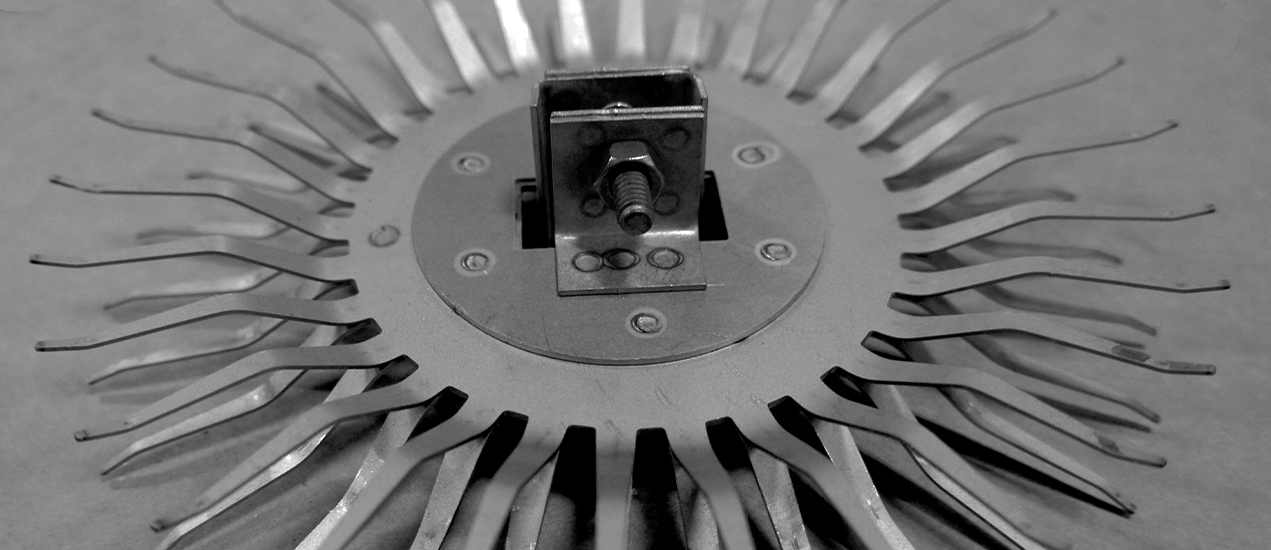
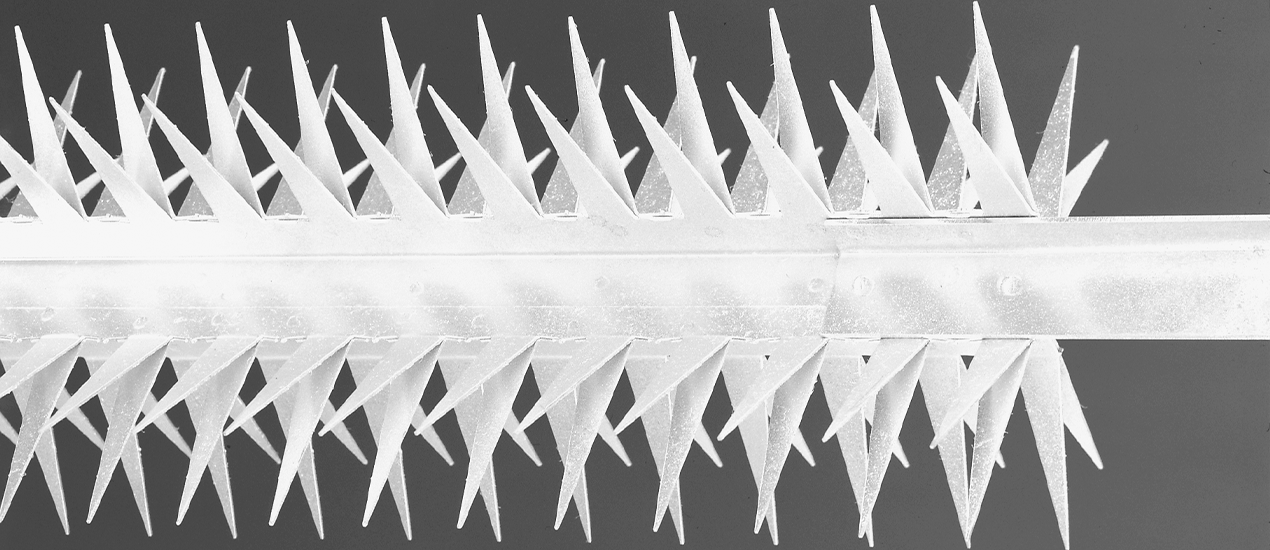
BENEFITS OF TITANIUM RACKS METAL FINISHING
- Corrosion Resistance:
Titanium is renowned for its remarkable resistance to corrosion. In metal finishing processes involving harsh chemicals, acids, and electrolytes, titanium racks stand up to these corrosive environments, ensuring longevity and reducing the need for frequent replacements. - Strength and Durability:
Despite being lightweight, titanium boasts a high strength-to-weight ratio, making it incredibly durable. titanium racks can withstand heavy loads and maintain their structural integrity over extended periods, even under strenuous conditions. - Temperature Stability:
Titanium retains its strength and resists oxidation even at high temperatures. This makes titanium racks ideal for processes that involve significant heat, such as electroplating and anodizing, where consistent performance is critical.
- Low Density:
The low density of titanium means that racks are lighter and easier to handle compared to those made from other metals. This property enhances operational efficiency, reducing the physical strain on workers and simplifying rack installation and removal.
- Non-Contaminating:
Titanium is non-reactive and does not contaminate the solutions it contacts. This ensures that the Metal Finishing process remains pure, preventing unwanted chemical reactions that could compromise the quality of the finished product.
- Cost-Effectiveness:
Although the initial investment in titanium racks may be higher than other materials, their durability and resistance to corrosion result in lower long-term costs. The extended lifespan and reduced maintenance requirements translate to significant savings over time.
technical resources
You’ll find product information, reactive metals information, corrosion charts, calculators and much more in the TITAN Technical Resource Center.
Design Considerations for titanium Racks
- Material: Racks are typically made from Stainless Steel, Titanium, or Aluminum Alloys that can withstand the chemical and thermal conditions of finishing processes.
- Insulation: In processes like anodizing, parts of the rack that should not conduct electricity are often coated with insulating materials.
- Contact Points: The design aims to minimize the number of contact points between the rack and the aluminum parts to prevent blemishes or defects in the finished surface.
- Adjustability: Many racks are adjustable to accommodate different shapes and sizes of aluminum parts, ensuring a secure fit and even exposure to the finishing process.
- Durability: Racks must be durable to endure repeated use and exposure to harsh chemicals and high temperatures without degrading.
maintenance and care
- Cleaning: Regular cleaning is essential to remove residues from previous finishing processes, which can affect the quality of subsequent treatments.
- Inspection: Racks should be inspected for wear and damage, particularly at contact points, to ensure they provide consistent results.
- Repair: Damaged racks should be repaired or replaced promptly to maintain the integrity of the finishing process.
CONTACT US
At RIGHTech Fabrications, your day-to-day needs only take days to deliver. From off-the-shelf to 100% custom, our capabilities and timely execution are unmatched. Our goal is to keep your production lines moving smoothly toward success.
Email: sales@rightechfabs.com
At RIGHTech Fabrications, your day-to-day needs only take days to deliver. From off-the-shelf to 100% custom, our capabilities and timely execution are unmatched. Our goal is to keep your production lines moving smoothly toward success.
Email: sales@rightechfabs.com