BASE METAL
PLATING
The Base Metal Plating industry is vital for numerous applications across different sectors, providing essential enhancements to the physical and chemical properties of metal products.
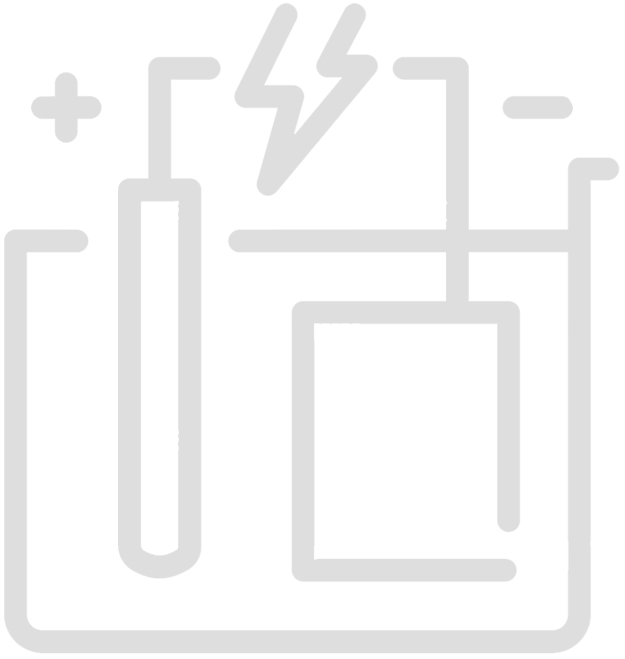
BASE METAL PLATING
INDUSTRY
Base Metal Plating involves the application of a metal coating to a base metal substrate. The base metal is typically a less expensive metal like Steel, Zinc, or Copper, and the plating metal is a more valuable or functional metal like Nickel, Chrome, or Gold. This process improves the surface properties of the base metal.
Metal Finishing encompasses a range of processes used to treat the surface of metal products to achieve desired characteristics such as improved appearance, corrosion resistance, electrical conductivity, wear resistance, and more.
processes in
base metal plating
Electroplating:
- Process: Involves the use of an electric current to deposit a metal coating on a conductive surface. The substrate metal serves as the cathode in an electrolytic cell, and the metal to be deposited serves as the anode.
- Common Metals: Nickel, Chromium, Copper, Zinc, Gold, Silver.
- Applications: Automotive parts, electronics, jewelry, hardware.
Electroless Plating:
- Process: Uses a chemical reduction reaction to deposit a metal layer without the use of an external electric current.
- Common Metals: Nickel, Copper.
- Applications: Circuit boards, hard disk drives, and other precision components where uniform coating is essential.
Hot-Dip Galvanizing:
- Process: Involves dipping steel or iron into molten zinc to form a strong, corrosion-resistant coating.
- Applications: Construction materials, outdoor structures, automotive bodies.
Anodizing:
- Process: Primarily used for aluminum, it involves an electrolytic passivation process to increase the thickness of the natural oxide layer on the metal’s surface.
- Applications: Aerospace parts, architectural elements, consumer electronics.
base metal plating
methods
Nickel Plating: Adds hardness, wear resistance, and corrosion resistance. It also provides a bright, smooth finish.
Chrome Plating: Often used for decorative purposes, providing a mirror-like finish and enhancing corrosion resistance and hardness.
Copper Plating: Provides an excellent conductive layer, often used in electronics and as a base layer for additional plating.
Zinc Plating: Offers good corrosion resistance, commonly used in automotive and industrial applications.
base metal plating
applications
Automotive: Enhancing the appearance and durability of car parts.
Aerospace: Improving the wear resistance and longevity of components exposed to extreme conditions.
Electronics: Providing conductive coatings for connectors, switches, and circuit boards.
Jewelry: Adding precious metal coatings to base metal jewelry items.
Construction: Protecting structural components from corrosion.
technical resources
You’ll find product information, reactive metals information, corrosion charts, calculators and much more in the TITAN Technical Resource Center.