ELECTROPLATING
The Electroplating industry plays a vital role in Metal Finishing by providing a wide range of functional and decorative surface treatments for metal components across various industries.
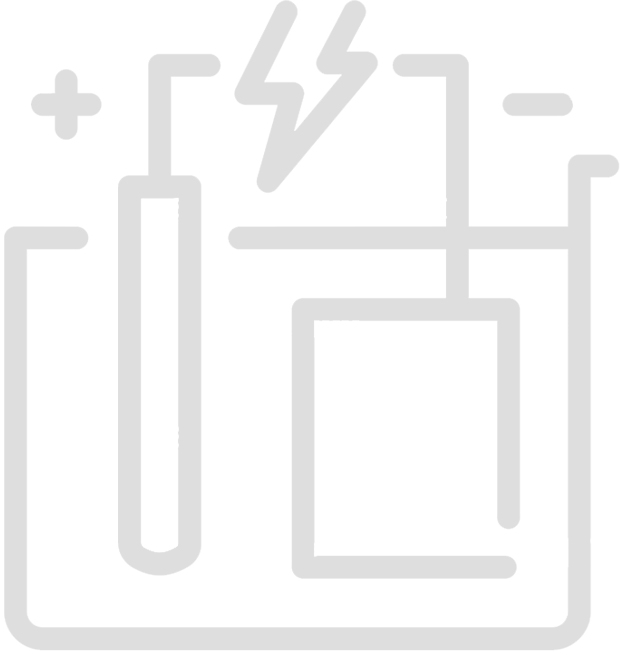
metal finishing electroplating industry
The Electroplating industry is a significant sector within the broader field of Metal Finishing. It involves the process of depositing a thin layer of metal onto a substrate through an electrochemical process. Electroplating is widely used across various industries to enhance the surface properties of metal components for both functional and decorative purposes.
Through ongoing innovation, technological advancements, and a commitment to sustainability, the Electroplating industry continues to evolve to meet the changing needs and challenges of modern manufacturing while ensuring high-quality, environmentally responsible plating solutions.
Electroplating process
Preparation: The substrate (the material to be plated) is cleaned thoroughly to remove any dirt, grease, or oxides that could interfere with the plating process.
Pre-Treatment: Depending on the substrate material, pre-treatment steps such as degreasing, pickling, and activation may be necessary to prepare the surface for plating.
Plating Bath Preparation: A plating bath is prepared by dissolving the plating metal (the metal to be deposited) in a suitable electrolyte solution. The bath typically contains metal salts and other additives to control plating characteristics.
Plating: The substrate is immersed in the plating bath and connected to the negative terminal (cathode) of a DC power supply. A conductive anode made of the plating metal is also immersed in the bath and connected to the positive terminal. When an electric current is passed through the bath, metal ions from the anode are attracted to the substrate’s surface, where they are reduced and deposited as a thin layer.
Rinsing and Finishing: After plating, the plated component is rinsed to remove any residual electrolyte and then may undergo post-treatment processes such as passivation, drying, or surface finishing.
electroPLATING considerations
Material Selection: The choice of plating metal and substrate material depends on the desired properties of the finished component, as well as factors such as cost, compatibility, and regulatory requirements.
Process Control: Maintaining precise control over plating parameters such as current density, bath composition, temperature, and agitation is essential to achieve uniform and high-quality plating results.
Quality Assurance: Quality control measures such as surface testing, thickness measurement, adhesion testing, and visual inspection are essential to ensure that plated components meet specified requirements and standards.
Energy Efficiency: Increasingly, efforts are being made to optimize electroplating processes for energy efficiency and sustainability by reducing resource consumption, minimizing waste generation, and implementing recycling and recovery measures.
electroPLATING
applications
Corrosion Protection: Electroplating with corrosion-resistant metals such as Zinc, Nickel, and Chromium provides a protective barrier against environmental degradation and extends the lifespan of metal components.
Decoration and Aesthetics: Electroplating with precious metals like Gold, Silver, and Platinum is commonly used for decorative purposes in jewelry, tableware, and architectural applications.
Electrical Conductivity: Electroplating can improve the electrical conductivity of metal components by depositing a thin layer of highly conductive metals such as Copper or Silver.
Wear and Abrasion Resistance: Electroplating with hard, wear-resistant metals such as chromium or tungsten carbide can increase the durability and lifespan of components subject to friction and abrasion.
Solderability and Bonding: Electroplating can enhance the solderability and bonding properties of metal surfaces, making them more compatible with soldering processes in electronics assembly.
technical resources
You’ll find product information, reactive metals information, corrosion charts, calculators and much more in the TITAN Technical Resource Center.